Cost Meaning:
- The Institute of Cost and Works Accountants of India, defines cost as “measurement, in monetary terms of the amount of resources used for the purpose of production of goods or rendering services”.
- Cost means the amount of expenditure incurred or attributable to a given thing. It is considered as the price to be paid to attain the objective.
- Cost is a resource sacrificed to achieve a certain objective.
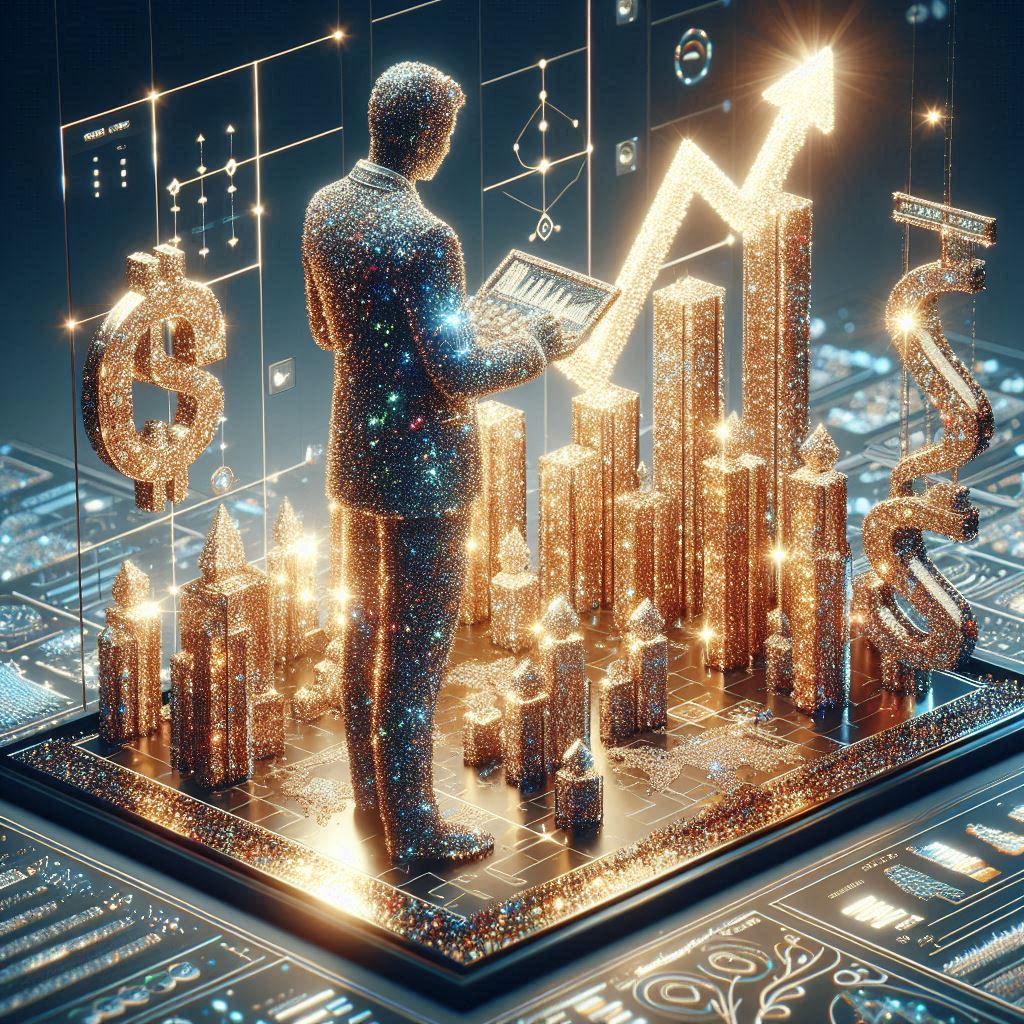
Cost accounting:
- Cost Accounting is the process of accounting for costs from the point at which the expenditure is incurred or generated to the acertainment of its ultimate relationship with various cost centres and cost units. It is a system of accounting which is concerned with output of costs of doing a certain activity which can be manufacturing or rendering services.
- Cost accounting is associated with determination of costs relating to a particular process, product or activity. It is the way to capture the total production cost of an organisation by taking into consideration the costs associated to each production process.
- The cost accounting is a significant system of ascertainments of costs, developed for management. It helps the internal management to take the best decisions, as the cost accounting provides with enough clarity pertaining to the costs associated to various processes.
- Cost accounting is a formal system of accounting by means of which costs of various products or services, are ascertained and controlled.
Whelden defines Cost Accounting as, “ Classifying, recording and appropriate allocation of expenditure for determination of costs of products or service and for the presentation of suitable arranged data for the purpose of control and guidance of management”.
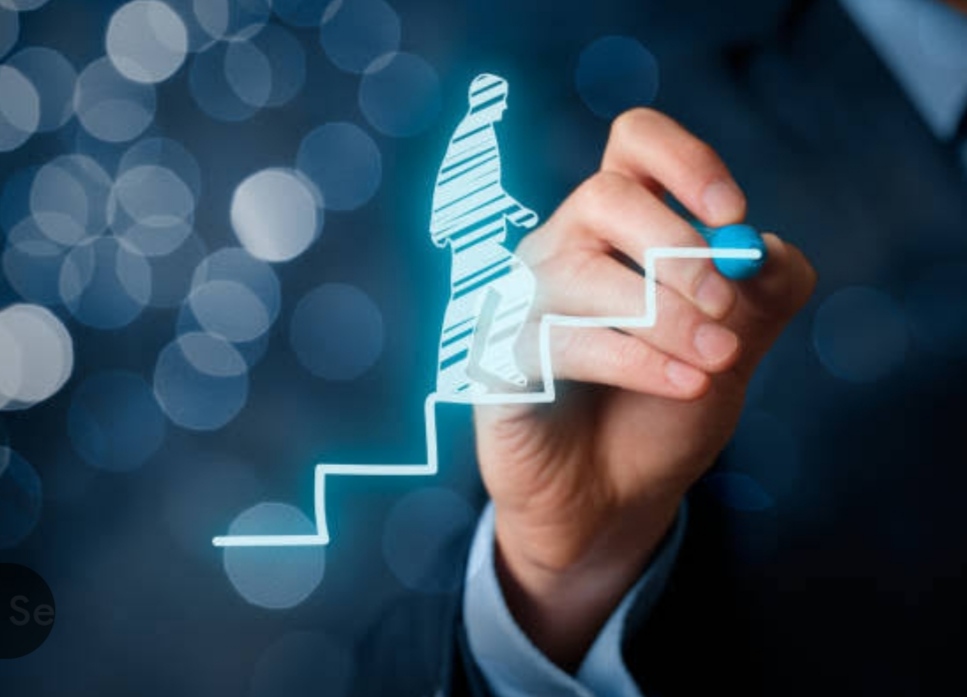
Objectives:
- This system of accounting helps to assertain and control the costs.
- It helps to classify the expenses i.e. material, labour, expenses.
- To allocate or charge the direct expenses to specific costs and to apportion common expenses to each product, contract or process on a suitable basis.
- It assists the management to take various business decisions.
- Indicates the management of any inefficiencies like wastage of raw materials, expenses.
- To determine the selling price.
- To advise the management on future policies regarding expansion, growth, capital Investments.
- Cost accounting helps in effective cost control.
- The figures of actual performance are compared with the targets to find out variation.
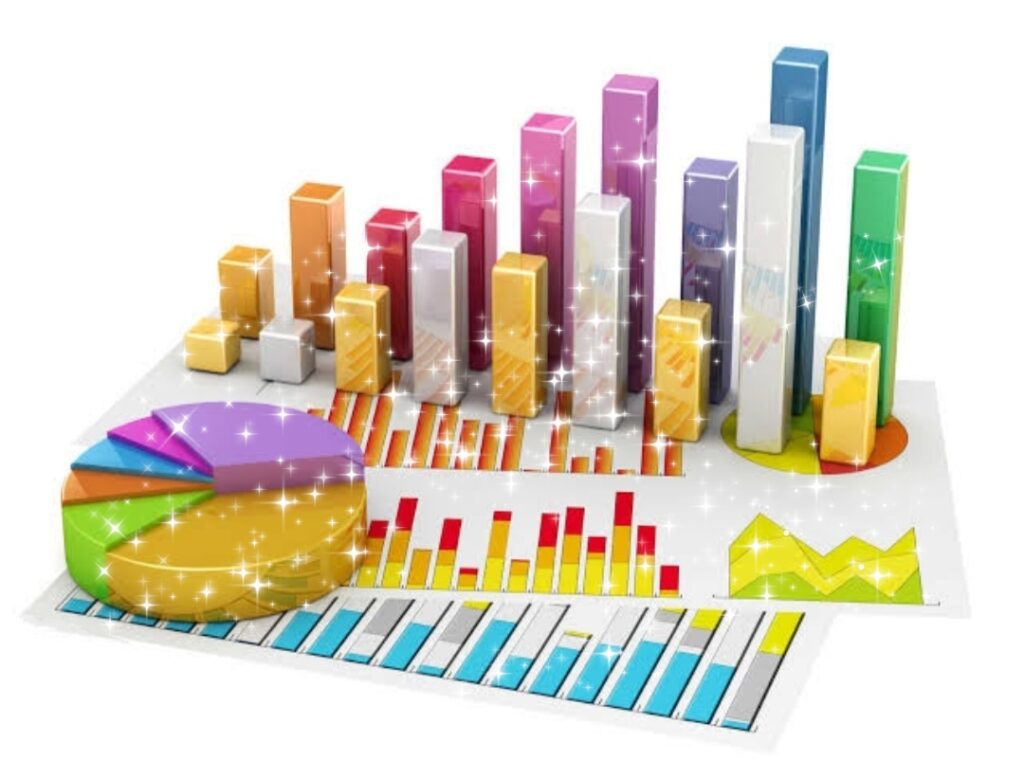
Elements of Costs:
To allocate or charge the direct expenses of specific costs such as raw material, labour, expenses that needs the classification of costs. The elements of costs are direct material, direct labour, direct expenses and overhead expenses.
What are direct costs?
Direct cost are those costs which are incurred for and conveniently identified with a particular cost unit process. this expenditure can be directly allocated to a particular job product or a process. For example, price paid to acquire raw materials, wages paid.
What are indirect costs?
Indirect costs are the general costs which are incurred for the benefit of a number of cost units, these are not conveniently identified with a particular cost unit. For example, Electricity, salaries, depreciation.
Material cost
Material cost refers to the material of any nature used for the purpose of production of a product or a service.
Direct material cost:
The direct material cost refers to the cost associated to acquisition of the basic raw materials which forms the part of the finished product. No finished product can be produced without the input of basic raw material. This cost is directly allocated to the product or process.
For example, materials specially acquired for manufacturing which passes from one process to another.
Indirect material cost:
Indirect material cost besides the direct material cost can not be allocated to the product or process directly. It refers to the material which cannot be allocated to the product but can be apportioned to the cost units. It is considered as a part of overheads as these are minor in nature. The cost of total quantity consumed for the period will be treated as indirect cost.
For example, grease, small tools, nails used in production of chairs, threats used in cloth making.
Labour cost
Labour cost is the cost of labour in the form of remuneration. There is a payment of salaries, bonuses and commission.
Direct labour cost:
This cost comprises of the wages paid to workers who involved in the manufacturing of the product. It consists of wages paid to those workers who are engaged in converting of raw materials into finished products. These workers directly handle machines on the production line. These are the labour involved in the actual production of the product.
For example, Factory workers.
Indirect labour cost:
This cost comprises of the wages paid to workers who are not involved in the manufacturing of the product. It is of a general nature and cannot be directly allocated to a particular cost unit.The indirect labour is not directly involved in the production operations but such labour helps or aids in the production processes. It is treated as a part of overheads.
For example, labour in shops, labour in Human Resource department.
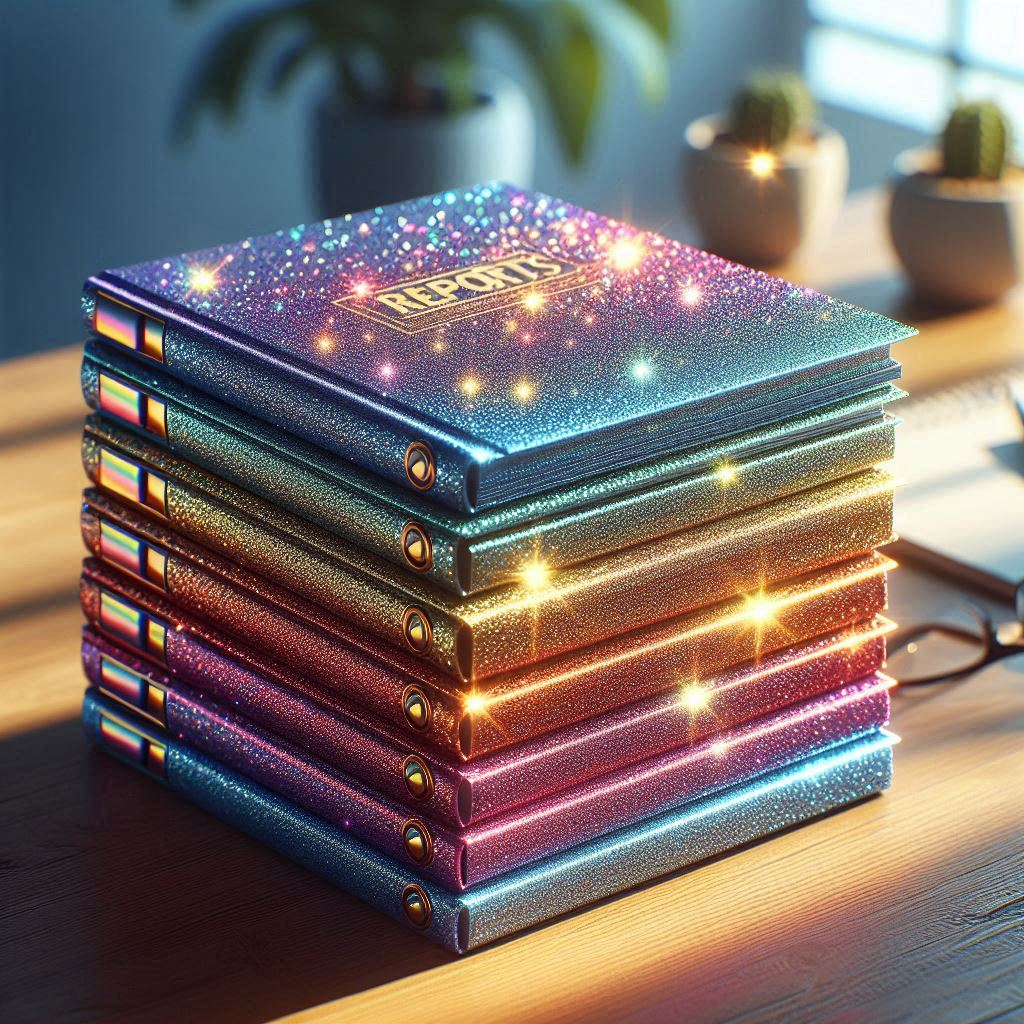
Expenses
All costs apart from material and labour are considered as expenses. These costs are again further classified into direct expenses and indirect expenses.
Direct expenses:
These are the expenses which are directly associated to the manufacturing line or which may be allocated to the product directly. These are the expenses which are specifically incurred in relation to a particular job or process. They are also known as chargeable expenses.
For example, conveyance expenses incurred to acquire a project, carriage paid to acquire materials for specific process.
Indirect expenses:
All indirect costs other than indirect materials and indirect labour costs, are known as indirect expenses. These are the expenses which are not directly associated to the manufacturing line or which may not be allocated to the product directly.
Overhead are subdivided as follows:
Factory Overheads: Also known as the manufacturing or production overheads, it comprises of all the costs of indirect material, indirect labour and other indirect expenses which are incurred in the factory. For example, factory rent, factory power, depreciation of factory machine.
Office or Administrative Overheads: All the indirect costs which are undertaken by the office for administration and management of the organisation. For example, rent,rates and taxes of premises, salaries of office staff.
Selling and Distribution Overheads: Indirect costs which are incurred in relation to the sales and distribution of the product. For example, advertising, conveyance, commission to sales agents.
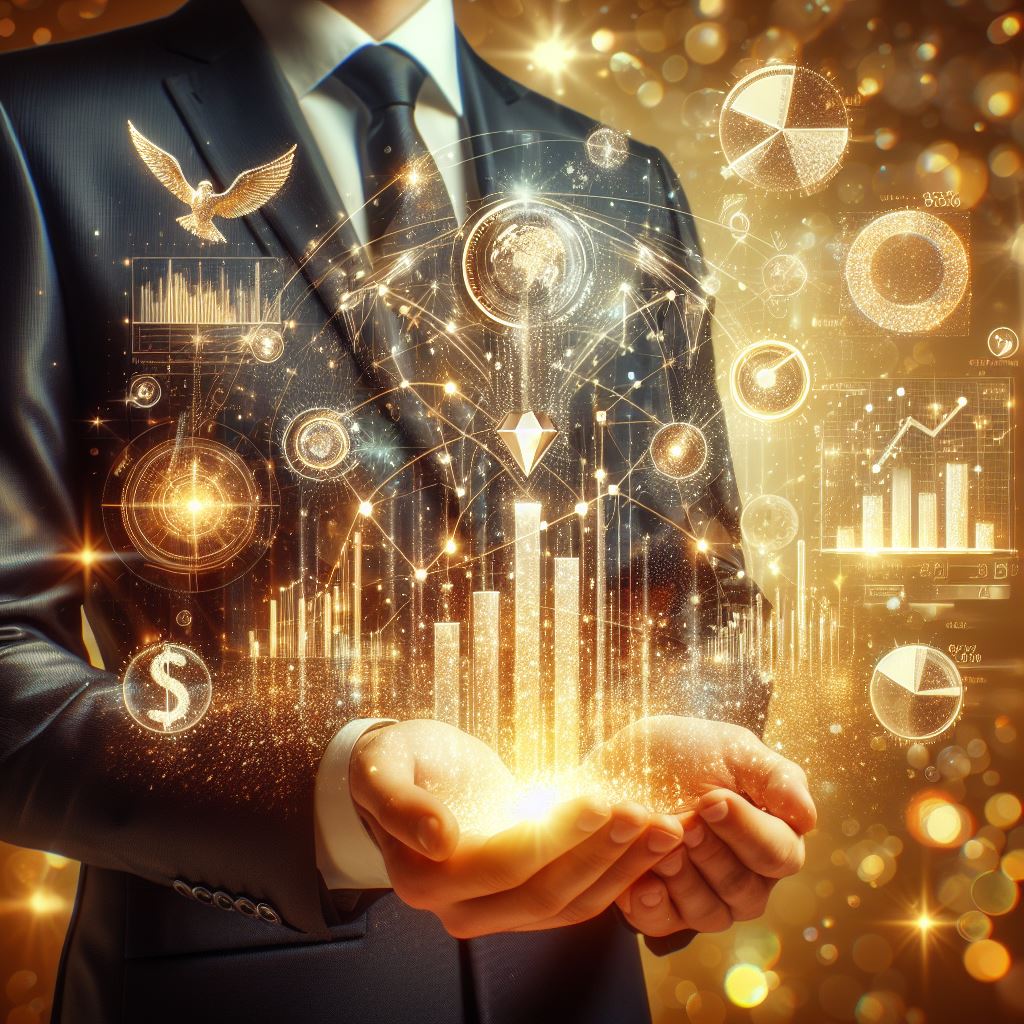